The MMC (micro milling center) and MMC H (micro milling center hydrostatic) series machines were developed according to the needs of ultra-precision milling. The difference between the two series is primarily the bearing type of the axis. While the MMC H series has hydrostatically linear bearings, the machines of the MMC series are equipped with aerostatic (air) bearings. The selection of the most suitable machine series / ultra-precision milling machine depends on the products to be manufactured.
The main application of the MMC series is primarily in the production of flat (plane) optical surfaces or precision parts by means of flycutting. With various accessories, the range of parts can be extended to microstructures, lenticular structures, spheres, polygons, etc.
The MMC H series has high speed tool spindles for the production (milling) of Microstructures, free-form surfaces, lens arrays, mold cavities. The machines are also available with a tilt / swivel unit for 5-axis UP machining of workpieces. Additionally or alternatively, of course, flycutter can be installed in the MMC H series.
MMC 600H
Control: | Delta Tau Power Pmac |
CNC-axes: | X-, Y-, and Z-axis, optional B, C and CC |
Bearing type: | hydrostatic (oil), CC air bearing |
Drive system: | linear motor X-, Y- and Z- axis, B and C with torque motors |
Travel: | X = 600 mm, Y = 220 mm, Z = 250 mm |
Speed: | up to 2000 mm/min (faster on request) |
Bearing type: | air bearing design |
Drive system: | torque motor |
Speed range: | 60.000, 80.000 or 100.000 RPM |
Milling head diameter:
: |
pneumatic collet or HSK 25 |
-
- 3D- touch probe
- C- axis, rotary / tilting table (tilt / swivel unit), CC- axis (6 axis)
- Minimum quantity lubrication
- Vacuum device for chip removal
- Tool Changer
- Additional Z- axis for Flycutting Spindle
MMC H
– micro milling
– hydrostatic (oil) bearing technology
– granite machine base
– process camera
– active machine leveling and vibration isolation system
– Automatictool changer
– Automatictool setting system
The MMC H (micro milling center hydrostatic) series machines were developed according to the needs of micro and ultra-precision multi-axis machining.
To create ideal conditions in terms of rigidity and damping for multi-axis machining, the series was equipped with hydrostatic (oil) bearings. By using diamond tools, optical surface quality can be achieved on a wide range of materials like crystals, nonferrous metals and plastics, even with complex geometries.
Similar to the MMC 600/900 air bearing machines, the basic setup can be equipped with various accessories. The basic setup consists of 3 linear axes and can be upgraded by additional rotary, tilt or spindle axes to 4, 5 or 6 axes. Accessories, like different spindles, vacuum chucks, palleting systems, 3D touch probes for workpiece measurement, tool changer and automated tool setting, allow an effective use of the machine.
Besides further accessories, there is the possibility to develop customized solutions, to adapt the machine to your needs. Please do not hesitate to contact us.
MMC 900H
– micro milling
– hydrostatic (oil) bearing technology
– granite machine base
– process camera
– active machine leveling and vibration isolation system
– Automatictool changer
– Automatictool setting system
The MMC H (micro milling center hydrostatic) series machines were developed according to the needs of micro and ultra-precision multi-axis machining.
To create ideal conditions in terms of rigidity and damping for multi-axis machining, the series was equipped with hydrostatic (oil) bearings. By using diamond tools, optical surface quality can be achieved on a wide range of materials like crystals, nonferrous metals and plastics, even with complex geometries.
Similar to the MMC 600/900 air bearing machines, the basic setup can be equipped with various accessories. The basic setup consists of 3 linear axes and can be upgraded by additional rotary, tilt or spindle axes to 4, 5 or 6 axes. Accessories, like different spindles, vacuum chucks, palleting systems, 3D touch probes for workpiece measurement, tool changer and automated tool setting, allow an effective use of the machine.
Besides further accessories, there is the possibility to develop customized solutions, to adapt the machine to your needs. Please do not hesitate to contact us.
Control: | Delta Tau Power Pmac |
CNC-axes: | X-, Y-, and Z-axis, optional B, C and CC |
Bearing type: | hydrostatic (oil), CC air bearing |
Drive system: | linear motor X-, Y- and Z- axis, B and C with torque motors |
Travel: | X = 900 mm, Y = 350 mm, Z = 250 mm |
Speed: | up to 2000 mm/min (faster on request) |
Bearing type: | air bearing design |
Drive system: | torque motor |
Speed range: | 60.000, 80.000 or 100.000 RPM |
Milling head diameter: | pneumatic collet or HSK 25 |
- 3D- touch probe
- C- axis, rotary / tilting table (tilt / swivel unit), CC- axis (6 axis) xxx
- Minimum quantity lubrication
- Vacuum device for chip removal
- Tool Changer
- Additional Z- axis for Flycutting Spindle
MMC H
MMC 600-900
Control: | Delta Tau Power Pmac |
CNC-axes: | X and Z, Y (optional), A, C (optional) |
Bearing type: | X-axis air bearing design , Z-axis roller-bearing |
Drive system: | DC servo motors |
Travel: | X = 600 mm, Z = 410 mm / X = 900 mm, Z = 410 mm |
Speed: | 1 mm / min up to 800 mm / min |
Bearing type: | air bearing design |
Drive system: | brushless DC motor |
Speed range: | 100 – 3000 RPM |
Milling head diameter: | Ø 200 mm up to Ø 500 mm |
- Workpiece thickness measurement (± 0,5 µm)
- Milling spindle for workpiece up to Ø 500 mm
- Minimum quantity lubrication
- Manually operated tilting axis (B-axis), 360°
- Interferometer: measuring area max. 12″
- Indexing head (air bearing) for polygon manufacture
- Rotary table (air bearing)
- Y-axis (roller- or air-bearing design)
MMC
– Aerostatic bearing technology
– Granite base
– Passive vibration isolation system
– Flatness: 0,1 μm within Ø 100 mm
– Roughness: 2 nm (Ra)
The MMC (micro milling center) series machines were developed according to the needs of ultra-precision milling. By using diamond tools, optical surface quality can be achieved on a wide range of materials like crystals, nonferrous metals and plastics.
The MMC 600/900 is the basis for a series of machines that, via several accessories and options, can be fully customized to individual needs. In the basic version the machine consists of a main X-axis featuring a linear air bearing (feed axis), a linear roller bearing Z-axis (infeed axis) and the milling spindle (air bearing) mounted on top of the Z-axis. The main application is face milling of optical and mechanical precision components.
Several accessories like a Y-axis, an A-axis and/or C-axis are available, thus expanding the range of machinable parts to microstructures, lenticular structures, spheres, polygons and so on.
Accessories, like vacuum chucks, different milling spindles, touch probes for part thickness measurement and even machine interferometers for insitu measurement of workpiece shape, make the MMC 600 and 900 machines an effective tool.
Besides further accessories, there is the possibility to make customized solutions, to adapt the machine to your needs.
MMC 5000
– Aerostatic bearing technology
– Granite base
– Passive vibration isolation system
– Flatness: 0.1 μm within 100 mm Ø
– Roughness: 2 nm (Ra)
The MMC (micro milling center) series machines were developed according to the needs of ultra-precision milling. By using diamond tools, optical surface quality can be achieved on a wide range of materials like crystals, nonferrous metals and plastics.
In the basic version the MMC 5000 consists of a main X-axis featuring a linear air bearing (feed axis), a linear roller bearing Z-axis (infeed axis) and the milling spindle (air bearing) mounted on top of the Z-axis. The main application is face milling of optical and mechanical precision components.
A Y-axis is available as an option. Another useful accessory is a second milling spindle, used perpendicular to the first one, thus allowing for the machining of two sides of a workpiece to perpendicularity in one setup.
Accessories, like vacuum chucks, different milling spindles, touch probes for part thickness measurement, machine interferometers and other sensors for insitu measurement of workpiece shape and roughness, make the MMC 5000 machines an effective tool.
In addition, various sensors are available for measuring of the workpiece geometry and surface quality during the manufacturing process. Besides further accessories, there is the possibility to make customized solutions, to adapt the machine to your needs.

Control: | Delta Tau Power Pmac |
CNC-axis: | X and Z, Y (optional), A, C (optional) |
Bearing type: | X-axis air bearing design , Z-axis roller-bearing |
Drive system: | Linear motor / servo motors |
Travel: | X = 5000 mm, Z = 410 mm |
Speed: | 1 mm / min up to 800 mm / min |
Bearing type: | air bearing design |
Drive system: | brushless DC motor |
Speed range: | 100 – 3000 RPM |
Milling head diameter: | Ø 200 mm – Ø 500 mm |
- Workpiece thickness measurement (± 0,5 μm)
- Milling spindle for workpiece up to Ø 500 mm
- Second milling spindle (90° tilted)
- Interferometer: measuring area max. 12″
- Sensors for insitu measurement of workpiece shape and roughness
- Indexing head (air bearing) for polygon manufacture
- Rotary table (air bearing)
- Y-axis (roller- air-bearing design)
MMC
Contact person
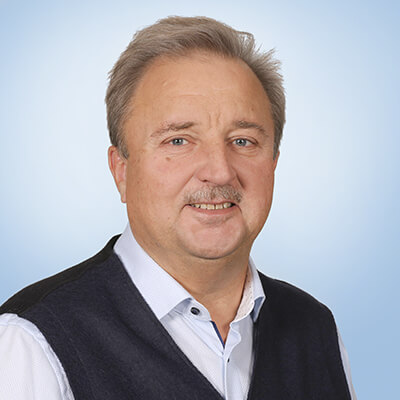
First name: | Richard |
Last name: | Widemann |
Responsible for: | UP-technology, service |
Phone: | +49 (0) 7552 – 4 05 99-80 |